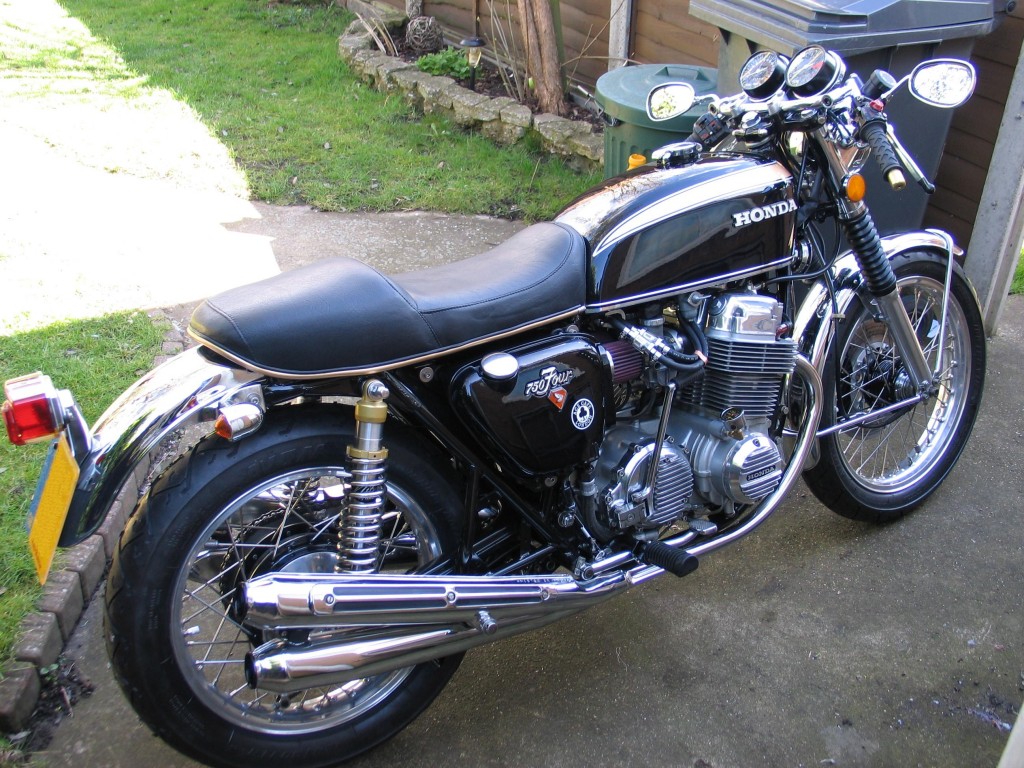
1. Colin’s midly customised Honda 750
Motorcycles through the ages have metamorphosized to produce what we have today. But sometimes this is not the principle of what the buyer wants, but it is close, hence people find Stotfold Engineering is the place to find that enhancement or modification to there custom bike to bring it up to there own specifications.
A customer, such as Johno, approached us with a host of modifications on his already factory customised Yamaha V4 bike. The order or schedule was to fit a tool and sat nav box in stainless 316 steel. This task was a very testing one as the box had a limited space to fit into and it had to be as large as possible so as to contain as much electrical and tooling aids as could be contained. The first thing was to ascertain what side profile would fit within the given space, i.e. if you looked at the side profile of the bike and looked at the gap where the box could be fitted. ‘What is the maximum size?’ The simplest plan is to make a cardboard profile and put a lot of thought into it, if you were to present me with a cardboard model you would have done 50% of the work, as all I would have to do is to replicate it in whatever material you wanted. Some custom parts are difficult to make models of, in this case it has to be made in the workshop out of metal tack welded together and holes drilled, tweaked and fitted to see if everything is in the right place. This process then forms the solid model that I would work from to produce the finished article.
Petrol tank customising is a tricky process as it is not a job that can be modelled in 3D. This type of work can only be marked out on the surface of the tank using tape or marker pen lines. Generally, customising tanks involves cutting apertures to take instruments such as speedometers (digital or mechanical) and things like scollops for clearance for Carburettor Bellmouths or velocity stacks.
There are instances when customising something cannot be modelled or marked out with any sort of precision, such as brake calliper mounts. The way I deal with a project like this is to take a plate of aluminium thicker than I need and roughly cut the profile but drill or tap the mounting holes precisely in there right positions. When this is done I mount the plate into its position and measure any offsets that are needed to bring the calliper into its right position in relation to the brake disc. The offsets are machined on the lean side so as not to throw any dimensions out leaving you having to use spacers or shims for alignments. We can always machine a few thou off to make everything look perfect. Remember that metal can’t be put back on to a machined surface without the completed job looking like it has been modified or adjusted with washers to take up inaccurate machining.
A customer approached us with a set of Webbs forks, he wanted us to use the existing design but using only billet machined parts to give a really modern twist on an old fashioned design. Of course with a job like this, models and marking out are not needed as we have the forks as our model.
Tank modified to take electronic instrument pannel
To fit this electronic pannel in the tank we had to produce a petrol proof opening with mounting brackets on the underside of the tank to support the electronic gauges. The oppening on the underneath of the tank obviously had to be big enough to take the electrical cables. The gauges had to fit exactly flush with the top of the tank.