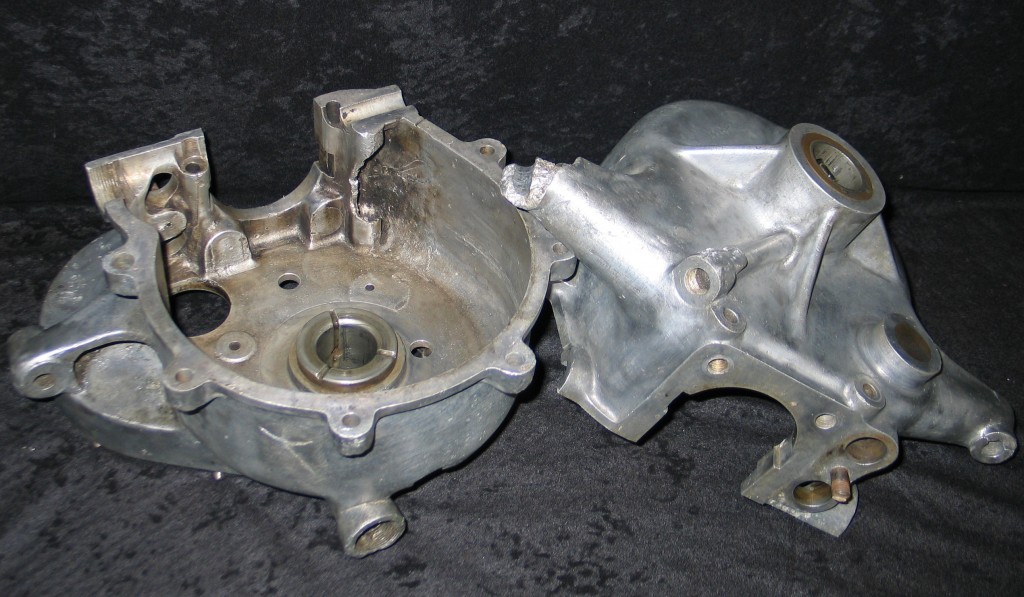
Damaged 1903 Renault crankcases in for repair
At Stotfold Engineering we do weld aluminium on a regular basis and often have customers come in to have their crankcases repaired on their classic motorcycle or car. However not all aluminium is easily repaired. Firstly lets have a look at it in more detail.
WHAT IS ALUMINIUM?; Aluminiumis the most common of the metal elements on the earth. It is used in almost all industries now, but its major use has been in the aircraft industry. Aluminium can be amalgamated with several other elements such as magnesium, sodium and zinc. These minerals give the aluminium a variety of different characteristics, changing the strength and corrosion resistance of pure aluminium.
WHY WOULD WE NEED TO WELD ALUMINIUM?; All metals used throughout industry have their weak points. Aluminium is no different. It cannot resist prolonged exposure to alkali’s and this causes the oxidised outer surface, which is acting as a protective layer from the elements to break down. Once the component starts to break down you have two choices; scrap or repair. In these days of recession repair is often the most cost effective course. Obviously, for example, to have a new crankcase cast and machined would be very expensive. However with the advent of modern materials and techniques you could end up with something better than the original. Straight replacement of parts with new is extensively employed in the aviation and MOD sector. In classic motorcycle and car restoration one tends to repair and restore due to maintaining the originality of as many parts as possible.
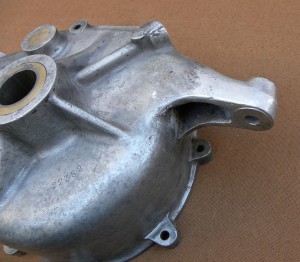
1. The finished repair on a engine mounting lug of a 1903 Renault
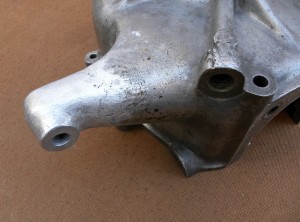
2. 1903 Renault fully restored engine mounting lug
HOW DO WE WELD ALUMINIUM? ;
TIG welding and gas welding are the most common types of aluminium welding in the restoration business. We use TIG welding for such things as crankcases or structural components and gas welding for body panels.
- Gas welding uses oxygen and hydrogen mixed from two separte gas bottles feed a nozzle that mixes the two together. This produces a flame ideal for welding aluminium sheet.
- TIG welding stands for Tungsten-arc Inert Gas. Firstly when aluminium castings are welded, like crankcases, it is important to first heat them in an oven to bring them nearer to the welding temperature. Then the TIG welding torch is applied with some aluminium filler rod to repair the damaged cases. Photos 1 & 2 show a repair to a 1903 Renault crankcase done by us. TIG welding is a mixture of electricity and gas. Electricity is passed through a tungsten tip shrouded by a ceramic tube. An inert gas called argon is fed into the tube from a bottle. This gas acts as a flux so that the oxides produced when heating aluminium are kept to a minium, so keeping the weld clean and flowing easily.
HOW DO WE PREPARE ALUMINIUM PARTS FOR WELDING?; Preparation is critical, with the main goal being to cut out all the rotten parts. Think of the oxidisation as a metallurgical cancer that needs to be cut out, so only good clean metal is showing. Removal of the oxidised aluminium can be achieved with a grinder, file or burr, or even a drill, as long as one cuts out all the rot to shinny clean aluminium. When this is achieved we can put a piece of aluminium plate, cut to the shape of the hole that is left, or simplify fill it with aluminium filler rod.
Safety Note: You should always where a mask when doing this, as aluminium dust is very bad for your body. Colin here at the workshop uses an army resparator which provides protection for the lungs, face and eyes. HOW WE DO IT IN PRACTICAL TERMS; Once we have received your damaged crankcases, for welding at our workshop, the first thing is to assess what needs cutting out and what needs filling with plate or solid welding rod. Any filler plates are made at this stage to fill larger holes or voids. The crankcase or part is then heated in an oven before employing the TIG welding process. Even bearing surfaces can be made up with rod.After welding and filling holes, the crankcase or parts is fettled to create a smooth invisible finish. Any bearing housings are machined to their original sizes. The parts are then aqua-blasted if required. WHAT ARE THE EFFECTS OF WELDING ALUMINIUM?; As long as the aluminium has been prepared correctly, pre-heated, and the correct rod has been selected for the grade of aluminium, there should be no adverse affects. WHAT ARE THE COMMON FAULTS IN ALUMINIUM WELDING?; Aluminium is fairly easy to weld provided the preheating and preparation process is followed. If you do try to weld a casting that has not been cut back to clean metal you will find the surrounding material next to the weld is peppered with small holes and the weld will be brittle at the join with the original material. The key to strength lies in penetration of the material, particularly on things like engine mounting bosses. If there is shallow penetration the part that has been welded will break of at the edge of the weld. By Terry Ives
Bellow is a crank case that has broken “i have marked out the originally broken spot with a marker”, as can be seen in the picture part has been welded and ground flush for an aesthetically pleasing look
You seem very knowledgable about this issue and it shows. Trust all your future posts turn out as well. Cheers!
I weld for a living and looking for a welding helemet is always a task . Godd stuff here and keep it up!
Ran across you site looking for a welding helmet of all things…LOL. Pretty goo site going on herer and will bookmark it.
You are a very creative blogger, and I absolutely love reading your posts.
Great site! Your style is so fresh in comparison to most other bloggers. Thank you for writing when you get the chance to, I’ll be sure to keep visiting!
Nice post…Thank you for sharing some good things!!
Aluminium welding and repair Stotfold Engineering Company LimitedI just stumbled upon your blog and wanted to say that I have really enjoyed reading your blog posts.6/5/2010
Interesting point of view on the subject, never thought I’d agree… But I do! Thanks again for the excellent information – Always the best, Joe.
Simple and effective, great work.
Your work has always been a great source of inspiration for me. I refer you blog to many of my friends as well.
I just wanted to comment your blog and say that I really enjoyed reading your blog post here. It was very informative and I also digg the way you write! Keep it up and I’ll be back to read more soon mate
Light enough to see the puddle and the path to weld. I use a 9 for all welding. Most people use a 10 to 12. You do not need a different shade for different types of welding.
been following ur website for three days. absolutely love your posts. btw i am doing research relating to this issue. do you happen to know any good sites or perhaps forums where I might get more information? many thanks.
I am so happy to read this. This is the kind of instruction that needs to be given and not the random misinformation that is at the other blogs. Looking through this great information.